نمودار تبدیل سنگ آهن به آهن خالص
ستاره | سرویس محتوای کمک درسی – آهن یکی از عناصر مهم درون کره زمین است که تقریبا بدون آن نمیتوان به زندگی ماشینی امروزی ادامه داد. این فلز که عملا به صورت خالص یافت نمیشود از جمله پرکابردترین عناصر در تمامی صنعتهاست. فولادها شاخه بزرگی از آلیاژهای آهنی هستند که وابستگی انسان به آنها غیرقابل انکار است. اما این عنصر حیاتی برای انسانها چگونه استخراج میگردد؟ مراحل تولید آهن و فرآیندهای مختلف آن به چه صورتی است؟
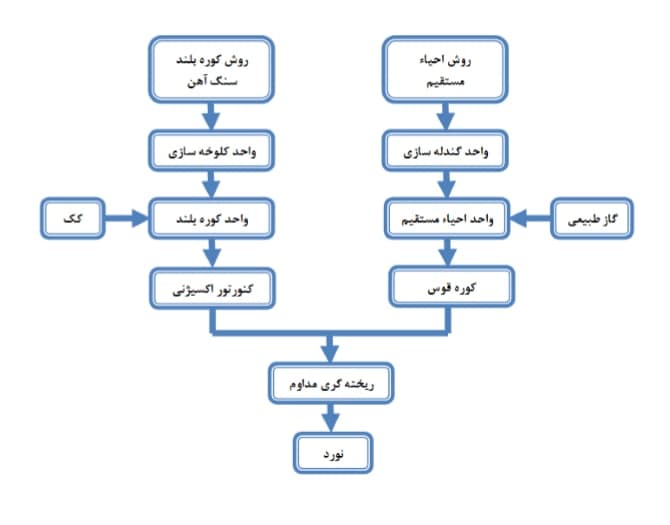
آهن چیست؟
آهن با نماد Fe و با عدد اتمی ۲۶ پس از آلومینیوم، فراوانترین عنصر روی کره زمین است. این فلز در در گروه ۸ و دوره ۴ جدول تناوبی قرار گرفته و نقطه ذوبی نزدیک به ۱۵۳۸ درجه سانتیگراد دارد. آهن بسادگی در مجاورت آب و هوا اکسید میشود و به همین دلیل، در اکثر موارد به صورت اکسید (سنگ معدن هماتیت Fe2O3) در طبیعت یافت میگردد.
ورق A516 گرید 70 نیز به نام ASME SA516-70 نامیده می شود. این گرید از ورق فولادی ، یک آلیاژ کربنی متوسط است که حاوی مقادیری از منگنز، فسفر، گوگرد و سیلیکون است.
بشر آهن را در حدود پنج هزار سال پیش کشف کرد. مصریان و جوامع واقع در بین النهرین از اولین تمدنهای قادر به استخراج سنگ آهن هستند.
بیشتر بخوانید:
مراحل تولید آهن و فرایندهای مختلف آن
فرایندهای انجام شده برای تولید آهن و استخراج آن از سنگ آهن پیچیده و یک واحد درسی دانشگاهی در رشته مهندسی مواد است. بنابراین تنها به بررسی مختصر مراحل تولید آهن و بیان آن به زبان ساده خواهیم پرداخت.
سنگ آهن: همانطور که گفته شد آهن به صورت خالص در زمین یافت نشده و تمامی موارد استخراج شده سنگ آهن هستند.
این سنگها ترکیبات مختلفی داشته و با توجه به نوع ترکیب آن فرایند استخراج و تخلیص سازی انجام میشود. از شناخته شدهترین سنگهای دارای ترکیب آهنی میتوان به هماتیت، مگنتیت، گوتیت، لیمونیت و … اشاره کرد. تفاوت در این سنگها به دلیل عدد اکسایس متفاوت آهن و تشکیل اکسیدهای گوناگون است.
فرایند تولید آهن در کورههای مخصوص ذوب آهن انجام میشود. به این صورت که:
۱. از بالای کوره بلند، کانی آهن (سنگ آهن)، کک و سنگ آهک را که گداز آور یا بار کوره نیز مینامند، وارد میکنند.
مواد گداز آور دو کار انجام میدهند:
- ذوب کردن ناخالصیهای موجود در سنگ آهن که نقطه ذوب آنها بالاتر از درجه حرارت معمولی کوره است.
- بعضی از عناصر که همزمان با سنگ آهن احیا میشود یا در آهن حل و یا با آن ترکیب شده و جدا کردن آن ممکن نمیگردد، مواد گداز آور با این ناخالصیها ، قبل از ترکیب با آهن ، ترکیب میگردند. نوع مواد گداز آور بستگی به ترکیب مواد متشکله بار کوره دارد.
مواد گداز آور:
- در صورتیکه سنگ آهن ، آهکی (قلیایی) باشد، ماده گداز آور باید اسیدی (مثل SiO2 سیلیس) باشد.
- در صورتیکه سنگ آهن ، سیلیسی (اسیدی) باشد، ماده گداز آور باید قلیایی (مثل سنگ آهک ، دولومیت و سنگهای فسفاته) باشد.
مراحل تولید آهن و فرایند مختلف آن
۲. از پایین کوره نیز جریان شدیدی از هوای گرم میدمند. این هوای گرم گاهی با اکسیژن تقویت میشود. هوای ورودی با کک یا همان کربن، ترکیب شده و مقدار قابل ملاحظهای گرما آزاد میکند. در این مرحله دمای کوره بالاترین مقدار یعنی حدود ۱۵۰۰ درجه سانتیگراد میرسد.
بازرگانی فولاد ایرانیان در حال حاضر بیش از ۵۰ نفر پرسنل از متخصصان حوزه صنعت را به صورت مستقیم با خود همراه کرده است.
توجه: برای بدست آوردن یک تن آهن خام ، حدود ۵ – ۶ تن هوا لازم است که این هوا از مخلوط دو گاز اکسیژن و ازت به نسبت ۱ و ۴ تشکیل شده است. در کورههای بلند جدید، هوا بوسیله کمپرسورهای توربینی به داخل کوره دمیده میشوند.
۳. دی اکسید کربن تشکیل شده افزایش پیدامی کند با کک ورودی واکنش داده مونو اکسیدکربن تشکیل میدهد
۴. منو اکسید کربن، اکسیژن را از اکسید آهن میگیرد و تشکیل آهن و دی اکسید کربن میدهد آهن ذوب شده به طرف ته کوره جاری میشود.
۵. سنگ آهک به زدودن ناخالصیها کمک میکند واکنش سنگ آهک با ناخالصیها خاکستر یا سرباره را تشکیل میدهد سرباره عمدتا کلسیم سلیکات است که روی آهن ذوب شده شناور است و فلز را از اکسید شدن به وسیله هوای ورودی حفظ میکند آهن و سرباره با هم مخلوط نمیشوند و دو لایه جداگانه در ته کوره تشکیل میدهند.
۶. سرباره در فواصل معین از کوره خارج میشود. از سرباره اغلب در ساخت جادهها استفاده میشود.
سرباره: عبارتست از ماده مذابی که بر اثر فعل و انفعال بین مواد گداز ، سنگ آهن ، سوخت و ناخالصیهای اکسید موجود در فلز بوجود میآید و در اثر این فعل انفعالات ، ناخالصیهایی که نباید در چدن وجود داشته باشد، از آهن خام جدا میشود.
۷. آهن نیز از راه دیگر خارج شده و بیشتر آهن به دست آمده از کوره در تهیه فولاد مورد استفاده قرار میگیرد.
فرایند احیای سنگ آهن و تبدیل آن به آهن خالص با فعل و انفعالات شیمیایی زیادی همراه است که به طور خلاصه برای تولید آهن واکنش زیر بایستی صورت پذیرد.
(مراحل واکنش) Fe2O3→Fe3O4→FeO→Fe
۳Fe2O3+CO↔۲Fe3O4+CO2
Fe3O4+CO↔۳FeO+CO2
Fe+CO↔Fe+CO2
طرح شماتیکی مراحل تولید آهن و فرایندهای مختلف آن به شرح زیر است:
مراحل تولید آهن
مطالب مرتبط:
مواد مذاب حاصل شامل آهن خام و سرباره میباشند که به سمت بوته کوره که قسمت تحتانی استوانه است جاری میشوند و بعلت وزن مخصوص متفاوت آهن و سرباره این دو از یکدیگر جدا میشوند و آهن توسط شیر تخلیه تحتانی و سرباره توسط شیر تخلیه فوقانی از انتهای کوره بلند تخلیه میشوند.
آهن خارج شده از قسمت تحتانی کوره بلند خالص نبوده و مقادیری Si، Mn، P، C نیز درون آن است.
در ایران به دلیل وجود معادن سنگ آهن فراوان همچون معدن سنگان خواف در استان خراسان رضوی و معدن چغارت در بافق یزد کارخانجات ذوب آهن و تولید آهن و فولاد نیز رونق یافتهاند. ذوب آهن اصفهان و در کنار آن فولاد مبارکه از مهمترین مراکز تولید آهن و فولاد در مرکز ایران هستند. آیا شما تابحال از نزدیک شاهد فرایند ذوب ریزی و عملیات کوره بلند در ذوب آهنها بودهاید؟ چگونه میتوان فرایند این کورهها را بهینه تر کرد؟ لطفا نظرات و پیشنهادات خود را در رابطه با مراحل تولید آهن و فرایندهای مختلف آن در انتهای همین مطلب با ما به اشتراک گذارید.
در مرکز آهن تضمین و اطمینان از کیفیت محصول در هنگام خرید را متعهد می شویم.