خمکاری لوله فلزی
خمکاری لوله فلزی فرآیندی حیاتی در صنایع گوناگون به معنای تغییر شکل دائمی لوله های فلزی به زوایای و شعاع های مشخص بدون تغییر در ضخامت دیواره یا ایجاد ترک و شکستگی است. این فرآیند امکان تولید قطعات پیچیده و دقیق را از لوله های اولیه فراهم می آورد و نقش کلیدی در ساخت سازه های فلزی سیستم های انتقال سیالات و تجهیزات صنعتی ایفا می کند. درک عمیق از اصول عملکرد دستگاه های خمکاری و عوامل مؤثر بر کیفیت خم برای مهندسان و تکنسین های فعال در این حوزه امری ضروری محسوب می شود.
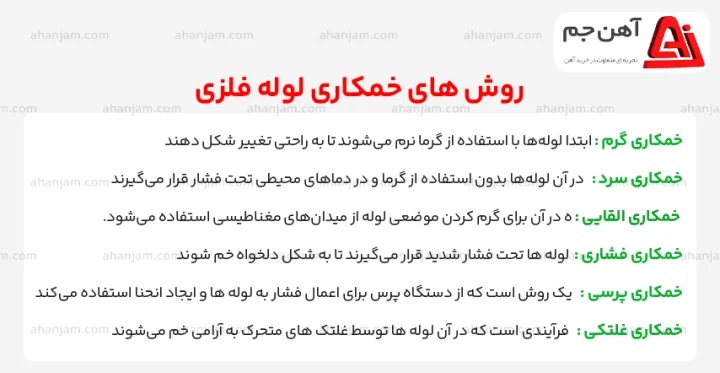
طبق نظر تازه ترین ها : مکاری لوله فلزی فرآیندی است که برای تغییر شکل لوله های فلزی به منظور ایجاد انحنا یا تغییر جهت در آنها استفاده میشود. این فرآیند میتواند به روشهای مختلفی مانند خمکاری گرم سرد فشاری یا با استفاده از ابزارهای خاص مانند دستگاههای CNC و پرسها انجام شود. خمکاری لوله های فلزی در صنایع مختلفی نظیر ساخت سازههای فلزی لوله کشی صنعتی خودروسازی و تولید تجهیزات انرژی کاربرد دارد. این فرآیند باید با دقت انجام شود تا از شکستن یا ترک خوردن لوله در هنگام خم شدن جلوگیری شود و لولهها بتوانند در کاربردهای خاص خود عملکرد مطلوبی داشته باشند. انتخاب روش خمکاری بستگی به جنس ضخامت قطر لوله و نوع انحنای مورد نظر دارد.
روش خمکاری لوله فلزی
دستگاه های خمکاری لوله با تنوع گسترده ای در طراحی و مکانیزم عملکرد همگی بر مبنای اعمال نیرو و گشتاور کنترل شده بر لوله به منظور ایجاد تغییر شکل پلاستیک در فلز عمل می کنند. اجزای اصلی این دستگاه ها بسته به نوع و کاربرد ممکن است متفاوت باشند اما اصول کارکرد مشترکی دارند که بر پایه دانش مکانیک مواد و مهندسی ساخت و تولید استوار است.
قالب خم لوله چیست ؟
قالب خم قلب دستگاه خمکاری لوله محسوب می شود و شکل نهایی خم را تعیین می کند. این قالب ها معمولاً از جنس فولادهای آلیاژی سخت شده و مقاوم به سایش ساخته می شوند تا در برابر نیروهای خمکاری و تماس مداوم با لوله دچار تغییر شکل یا آسیب نشوند. طراحی دقیق قالب خم با در نظر گرفتن شعاع خم مورد نظر زاویه خم و مشخصات لوله (قطر ضخامت دیواره جنس) از اهمیت بالایی برخوردار است.
اصول کارکرد
قالب خم لوله را در حین فرآیند خمکاری هدایت و پشتیبانی می کند. شکل هندسی قالب مسیر حرکت لوله را تعیین کرده و با اعمال فشار مناسب تغییر شکل پلاستیک را در ناحیه خم ایجاد می کند. طراحی قالب باید به گونه ای باشد که از ایجاد عیوب خمکاری مانند چروکیدگی (wrinkling) نازک شدن دیواره (wall thinning) و پارگی (fracture) جلوگیری شود.
مندرل (Mandrel)
مندرل یک ابزار استوانه ای شکل است که به صورت داخلی در لوله قرار می گیرد و نقش حیاتی در حفظ شکل و جلوگیری از تغییر شکل نامطلوب لوله در حین خمکاری به ویژه در خمکاری لوله های با دیواره نازک یا شعاع خم کوچک ایفا می کند. مندرل ها انواع مختلفی دارند از جمله مندرل های توپی (ball mandrel) مندرل های شاخه ای (segmented mandrel) و مندرل های پلاگ (plug mandrel) که هر کدام برای کاربردهای خاصی مناسب هستند.
اصول کارکرد : مندرل با پشتیبانی داخلی از دیواره لوله در ناحیه خم از فروپاشی یا تغییر شکل مقطع لوله جلوگیری می کند. به ویژه در فرآیندهای خمکاری با شعاع کم که تنش های زیادی در دیواره لوله ایجاد می شود مندرل نقش بسیار مهمی در حفظ کیفیت خم و جلوگیری از ایجاد عیوب دارد. انتخاب نوع مناسب مندرل و تنظیم دقیق موقعیت آن نسبت به قالب خم از عوامل کلیدی در دستیابی به خمکاری با کیفیت بالا است.
فک فشار (Pressure Die)
فک فشار قطعه ای است که در مقابل قالب خم قرار می گیرد و با اعمال فشار کنترل شده لوله را به سمت قالب خم هدایت می کند. فک فشار به همراه قالب خم نیروی خمکاری لازم را به لوله اعمال کرده و فرآیند تغییر شکل را کنترل می کند. طراحی فک فشار باید به گونه ای باشد که از لغزش لوله در حین خمکاری جلوگیری کرده و توزیع یکنواخت فشار را بر سطح لوله تضمین کند.
اصول کارکرد : فک فشار با ایجاد اصطکاک کافی بین لوله و قالب خم مانع از حرکت لوله به سمت عقب در حین خمکاری می شود. فشار اعمالی توسط فک فشار باید به دقت کنترل شود تا از آسیب به سطح لوله و ایجاد عیوب احتمالی جلوگیری شود. در برخی از دستگاه های خمکاری پیشرفته فک فشار متحرک (boost pressure die) استفاده می شود که با حرکت همزمان با لوله در حین خمکاری به بهبود کیفیت خم و کاهش نیروی خمکاری کمک می کند.
گیره (Clamp)
گیره ابزاری است که لوله را در موقعیت ثابت نگه می دارد و از حرکت ناخواسته آن در حین فرآیند خمکاری جلوگیری می کند. گیره ها معمولاً از جنس فولاد ساخته می شوند و طراحی آن ها باید به گونه ای باشد که لوله را به طور محکم و ایمن نگه دارد بدون اینکه به سطح لوله آسیب برساند. انواع مختلفی از گیره ها وجود دارد از جمله گیره های دستی پنوماتیکی و هیدرولیکی که بسته به نوع دستگاه خمکاری و نیازهای تولید انتخاب می شوند.
اصول کارکرد : گیره با ایجاد نیروی نگه دارنده قوی اطمینان حاصل می کند که لوله در موقعیت دقیق خود باقی می ماند و فرآیند خمکاری با دقت و کنترل انجام می شود. موقعیت و طراحی گیره باید به گونه ای باشد که با سایر اجزای دستگاه خمکاری تداخل نداشته باشد و دسترسی آسان به لوله را برای بارگذاری و تخلیه فراهم کند.
سیستم محرکه و کنترل (Drive and Control System)
سیستم محرکه و کنترل مسئول تأمین نیروی لازم برای خمکاری و کنترل دقیق حرکت اجزای دستگاه است. این سیستم ها می توانند هیدرولیکی پنوماتیکی الکترومکانیکی یا ترکیبی از آن ها باشند. سیستم های کنترل پیشرفته مانند کنترل عددی کامپیوتری (CNC) امکان برنامه ریزی دقیق و تکرارپذیری بالای فرآیند خمکاری را فراهم می کنند.
اصول کارکرد : سیستم محرکه نیروی لازم برای حرکت قالب خم فک فشار و مندرل را تأمین می کند. سیستم کنترل با استفاده از سنسورها و الگوریتم های کنترلی موقعیت سرعت و نیروی اعمالی را به دقت تنظیم و کنترل می کند. در دستگاه های CNC برنامه های خمکاری از پیش تعریف شده به سیستم کنترل داده می شوند و دستگاه به صورت خودکار فرآیند خمکاری را با دقت و تکرارپذیری بالا انجام می دهد.
کاربردهای خمکاری لوله فلزی
خمکاری لوله فلزی به دلیل قابلیت شکل دهی دقیق و کارآمد لوله ها در صنایع متنوعی کاربرد دارد. این فرآیند امکان تولید قطعات پیچیده با هندسه های گوناگون را فراهم می آورد و در ساخت محصولات و سیستم های مختلف نقش اساسی ایفا می کند.
صنعت خودرو
در صنعت خودرو خمکاری لوله فلزی کاربردهای گسترده ای دارد. سیستم های اگزوز سیستم های ترمز سیستم های سوخت رسانی و سازه های شاسی خودرو همگی از قطعات خمکاری شده لوله تشکیل شده اند. لوله های خمکاری شده در این صنعت باید از استحکام و دقت بالایی برخوردار باشند تا عملکرد ایمن و قابل اعتماد خودرو را تضمین کنند. به عنوان مثال سیستم های اگزوز خودرو از لوله های فولادی ضد زنگ خمکاری شده با دقت بالا ساخته می شوند تا در برابر حرارت و خوردگی مقاوم باشند و عملکرد بهینه سیستم اگزوز را فراهم کنند.
صنعت هوافضا
صنعت هوافضا به دلیل نیاز به قطعات سبک و مقاوم با دقت ابعادی بالا از خمکاری لوله فلزی به طور گسترده استفاده می کند. سیستم های هیدرولیک هواپیما سیستم های سوخت رسانی و سازه های داخلی کابین از لوله های آلومینیومی تیتانیومی و فولادی آلیاژی خمکاری شده تشکیل شده اند. در این صنعت استانداردهای کیفیت بسیار سختگیرانه ای اعمال می شود و فرآیند خمکاری باید با دقت و کنترل بسیار بالا انجام شود تا قطعات مطابق با مشخصات فنی مورد نظر تولید شوند.
صنعت ساختمان و سازه
در صنعت ساختمان و سازه لوله های فلزی خمکاری شده برای ساخت سازه های فلزی نرده ها لوله های انتقال آب و گاز و سیستم های تهویه مطبوع به کار می روند. لوله های فولادی خمکاری شده در ساخت اسکلت فلزی ساختمان ها پل ها و سایر سازه های بزرگ نقش اساسی دارند. همچنین لوله های مسی و آلومینیومی خمکاری شده در سیستم های لوله کشی ساختمان و سیستم های HVAC (Heating, Ventilation, and Air Conditioning) به طور گسترده استفاده می شوند.
صنعت نفت و گاز
صنعت نفت و گاز یکی از بزرگترین مصرف کنندگان لوله های فلزی خمکاری شده است. خطوط لوله انتقال نفت و گاز سکوهای نفتی پالایشگاه ها و تاسیسات پتروشیمی همگی از شبکه های پیچیده ای از لوله های خمکاری شده تشکیل شده اند. لوله های مورد استفاده در این صنعت باید در برابر فشار بالا دماهای شدید و محیط های خورنده مقاوم باشند. خمکاری لوله های با قطر بزرگ و ضخامت دیواره بالا در این صنعت از اهمیت ویژه ای برخوردار است و نیازمند استفاده از دستگاه ها و فناوری های پیشرفته است.
صنعت پزشکی
در صنعت پزشکی لوله های فلزی خمکاری شده در ساخت تجهیزات پزشکی ایمپلنت های جراحی و ابزارهای دقیق پزشکی کاربرد دارند. لوله های فولادی ضد زنگ و تیتانیومی خمکاری شده به دلیل زیست سازگاری و مقاومت به خوردگی در ساخت ایمپلنت های جراحی و ابزارهای پزشکی مورد استفاده قرار می گیرند. دقت ابعادی و کیفیت سطح بالای قطعات خمکاری شده در این صنعت از اهمیت بسیار زیادی برخوردار است.
استانداردها در خمکاری لوله فلزی
صنعت خمکاری لوله فلزی تحت تأثیر استانداردهای بین المللی و فناوری های پیشرفته به طور مداوم در حال پیشرفت و بهبود است. استانداردها چارچوبی برای تضمین کیفیت و ایمنی فرآیند خمکاری و محصولات نهایی ارائه می دهند در حالی که فناوری های پیشرفته امکان افزایش دقت سرعت و کارایی فرآیند را فراهم می کنند.
استانداردهای بین المللی
استانداردهای بین المللی متعددی در زمینه خمکاری لوله فلزی وجود دارند که مشخصات فنی روش های آزمون و الزامات کیفی مربوط به فرآیند خمکاری و محصولات خمکاری شده را تعیین می کنند. برخی از مهم ترین این استانداردها عبارتند از :
- ISO ۹۰۰۱ : استاندارد سیستم مدیریت کیفیت که الزامات مربوط به سیستم مدیریت کیفیت سازمان های فعال در زمینه خمکاری لوله را تعیین می کند.
- ISO/TS ۱۶۹۴۹ : استاندارد سیستم مدیریت کیفیت ویژه صنایع خودرو که الزامات خاص مربوط به فرآیند خمکاری لوله در صنعت خودرو را پوشش می دهد.
- ASTM B۲۱۰ : استاندارد مشخصات فنی برای لوله های آلومینیومی کشیده شده که الزامات مربوط به ابعاد خواص مکانیکی و روش های آزمون لوله های آلومینیومی مورد استفاده در خمکاری را مشخص می کند.
- ASTM A۵۳ : استاندارد مشخصات فنی برای لوله های فولادی سیاه و گالوانیزه جوشکاری شده و بدون درز که الزامات مربوط به لوله های فولادی پرکاربرد در صنعت را تعیین می کند.
- EN ۱۰۲۱۷ : استاندارد اروپایی برای لوله های فولادی جوشکاری شده برای کاربردهای تحت فشار که الزامات مربوط به لوله های فولادی مورد استفاده در سیستم های تحت فشار را مشخص می کند.
رعایت این استانداردها تضمین می کند که فرآیند خمکاری لوله مطابق با الزامات کیفی و ایمنی انجام شده و محصولات نهایی از کیفیت و عملکرد مورد انتظار برخوردار باشند.
انواع خمکاری لوله فلزی
فناوری های پیشرفته نقش کلیدی در بهبود فرآیند خمکاری لوله و افزایش کارایی و دقت آن ایفا می کنند. برخی از مهم ترین این فناوری ها عبارتند از :
- خمکاری CNC (Computer Numerical Control) : دستگاه های خمکاری CNC با استفاده از سیستم های کنترل کامپیوتری امکان برنامه ریزی دقیق و تکرارپذیری بالای فرآیند خمکاری را فراهم می کنند. این دستگاه ها قادر به تولید قطعات پیچیده با هندسه های دقیق و تلرانس های ابعادی سختگیرانه هستند.
- خمکاری رباتیک (Robotic Bending) : استفاده از ربات های صنعتی در فرآیند خمکاری لوله امکان اتوماسیون کامل فرآیند افزایش سرعت تولید و بهبود ایمنی را فراهم می کند. ربات ها قادر به انجام خمکاری های پیچیده و دشوار با دقت و تکرارپذیری بالا هستند.
- خمکاری القایی (Induction Bending) : در این روش از حرارت القایی برای گرم کردن موضعی لوله در ناحیه خم استفاده می شود. حرارت موضعی باعث کاهش نیروی خمکاری و افزایش قابلیت شکل پذیری لوله می شود. خمکاری القایی به ویژه برای خمکاری لوله های با قطر بزرگ و ضخامت دیواره بالا مناسب است.
- خمکاری با کمک لیزر (Laser Assisted Bending) : در این روش از لیزر برای گرم کردن موضعی لوله در ناحیه خم استفاده می شود. خمکاری با کمک لیزر امکان خمکاری دقیق و ظریف لوله های با دیواره نازک و مواد حساس به حرارت را فراهم می کند.
- شبیه سازی فرآیند خمکاری (Bending Process Simulation) : نرم افزارهای شبیه سازی فرآیند خمکاری امکان پیش بینی رفتار مواد در حین خمکاری شناسایی عیوب احتمالی و بهینه سازی پارامترهای فرآیند را فراهم می کنند. استفاده از این نرم افزارها به کاهش هزینه ها و زمان تولید و بهبود کیفیت خمکاری کمک می کند.
محدودیت های فنی خمکاری لوله فلزی
فرآیند خمکاری لوله با وجود پیشرفت های چشمگیر همچنان با چالش ها و محدودیت های فنی روبرو است. درک این چالش ها و محدودیت ها برای مهندسان و تکنسین های فعال در این حوزه امری ضروری است تا بتوانند راه حل های مناسب برای غلبه بر آن ها را پیدا کنند.
برگشت فنری (Springback)
برگشت فنری پدیده ای است که در آن لوله پس از اتمام فرآیند خمکاری و برداشتن نیرو به حالت اولیه خود باز می گردد. این پدیده ناشی از خاصیت الاستیک مواد فلزی است و باعث ایجاد اختلاف بین زاویه خم مورد نظر و زاویه خم واقعی می شود. برگشت فنری به ویژه در خمکاری مواد با استحکام بالا و شعاع خم کوچک بیشتر مشهود است. جبران برگشت فنری یکی از چالش های اصلی در خمکاری لوله است و نیازمند استفاده از روش های جبران سازی مناسب مانند خمکاری بیش از حد (overbending) یا استفاده از قالب های جبران کننده (springback compensation dies) است.
نازک شدن دیواره (Wall Thinning) و چروکیدگی (Wrinkling)
در حین فرآیند خمکاری دیواره لوله در ناحیه بیرونی خم تحت کشش قرار می گیرد و ممکن است نازک شود. در مقابل دیواره لوله در ناحیه داخلی خم تحت فشار قرار می گیرد و ممکن است چروکیده شود. نازک شدن دیواره می تواند منجر به کاهش استحکام و مقاومت لوله در ناحیه خم شود در حالی که چروکیدگی می تواند باعث ایجاد تمرکز تنش و کاهش کیفیت سطح لوله شود. جلوگیری از نازک شدن دیواره و چروکیدگی نیازمند کنترل دقیق پارامترهای فرآیند خمکاری طراحی مناسب قالب ها و مندرل و استفاده از روش های خمکاری مناسب است.
محدودیت های مواد
قابلیت خمکاری مواد مختلف متفاوت است. برخی از مواد مانند فولادهای نرم و آلومینیوم به راحتی خم می شوند در حالی که برخی دیگر مانند فولادهای با استحکام بالا و تیتانیوم خمکاری دشوارتری دارند و نیازمند استفاده از دستگاه ها و روش های خاص هستند. انتخاب مواد مناسب برای کاربردهای خمکاری و در نظر گرفتن محدودیت های خمکاری مواد مختلف از اهمیت بالایی برخوردار است.
دقت ابعادی و کیفیت سطح
دستیابی به دقت ابعادی بالا و کیفیت سطح مطلوب در قطعات خمکاری شده همواره یک چالش فنی بوده است. عواملی مانند برگشت فنری ارتعاشات دستگاه و کیفیت مواد اولیه می توانند بر دقت ابعادی و کیفیت سطح قطعات خمکاری شده تأثیر بگذارند. استفاده از دستگاه های خمکاری دقیق قالب های با کیفیت بالا و روش های کنترل کیفیت مناسب برای دستیابی به دقت ابعادی و کیفیت سطح مطلوب ضروری است.
نکات کلیدی خمکاری لوله
بهینه سازی فرآیند خمکاری لوله به منظور افزایش کیفیت خم کاهش هزینه ها و افزایش بهره وری از اهمیت بالایی برخوردار است. رعایت نکات کلیدی در طراحی فرآیند انتخاب تجهیزات و اجرای عملیات خمکاری می تواند به بهبود عملکرد و دستیابی به نتایج مطلوب کمک کند.
طراحی مناسب قالب ها و مندرل
طراحی دقیق و مهندسی قالب ها و مندرل نقش اساسی در کیفیت خمکاری دارد. قالب ها باید با شعاع خم و زاویه خم مورد نظر و با در نظر گرفتن مشخصات لوله (قطر ضخامت دیواره جنس) طراحی شوند. مندرل باید به گونه ای انتخاب شود که پشتیبانی کافی از دیواره لوله در ناحیه خم را فراهم کند و از تغییر شکل نامطلوب لوله جلوگیری نماید. استفاده از مواد با کیفیت بالا و روش های ساخت دقیق برای قالب ها و مندرل به افزایش عمر مفید و بهبود کیفیت خمکاری کمک می کند.
انتخاب مواد اولیه مناسب
انتخاب مواد اولیه مناسب با توجه به کاربرد مورد نظر و الزامات خمکاری از اهمیت بالایی برخوردار است. مواد باید از قابلیت خمکاری مناسب برخوردار باشند و خواص مکانیکی و شیمیایی مورد نیاز را برآورده کنند. بررسی مشخصات فنی مواد و انجام آزمایش های خمکاری اولیه قبل از شروع تولید انبوه توصیه می شود.
کنترل دقیق پارامترهای فرآیند
کنترل دقیق پارامترهای فرآیند خمکاری مانند سرعت خمکاری نیروی خمکاری فشار فک فشار و موقعیت مندرل برای دستیابی به کیفیت خم مطلوب ضروری است. استفاده از سیستم های کنترل پیشرفته مانند CNC و نظارت مداوم بر پارامترهای فرآیند به حفظ کیفیت و تکرارپذیری فرآیند خمکاری کمک می کند.
استفاده از روانکاری مناسب
روانکاری مناسب در حین فرآیند خمکاری می تواند به کاهش اصطکاک بین لوله و قالب ها کاهش نیروی خمکاری و بهبود کیفیت سطح خم کمک کند. انتخاب روانکار مناسب با توجه به جنس لوله و شرایط خمکاری از اهمیت بالایی برخوردار است. روغن های خمکاری گریس ها و پوشش های روانکار جامد از جمله روانکارهای رایج در خمکاری لوله هستند.
آموزش و مهارت اپراتور
مهارت و تجربه اپراتور دستگاه خمکاری نقش مهمی در کیفیت و کارایی فرآیند خمکاری دارد. آموزش مناسب اپراتورها در زمینه اصول خمکاری تنظیم دستگاه و رفع عیوب احتمالی به بهبود عملکرد و کاهش ضایعات کمک می کند. برگزاری دوره های آموزشی تخصصی و ارتقاء دانش فنی اپراتورها توصیه می شود.
نگهداری و بازرسی دوره ای دستگاه
نگهداری و بازرسی دوره ای دستگاه خمکاری به منظور اطمینان از عملکرد صحیح و ایمن دستگاه و جلوگیری از خرابی های ناگهانی ضروری است. بازرسی منظم اجزای دستگاه روانکاری قطعات متحرک و تعویض قطعات فرسوده به افزایش عمر مفید دستگاه و حفظ کیفیت خمکاری کمک می کند.
نتیجه گیری
خمکاری لوله فلزی فرآیندی کلیدی در صنایع مدرن است که امکان شکل دهی دقیق و کارآمد لوله های فلزی را برای کاربردهای متنوع فراهم می آورد. درک عمیق از اصول عملکرد اجزای دستگاه خمکاری چالش ها و محدودیت های فنی و روش های بهینه سازی فرآیند برای مهندسان و تکنسین های فعال در این حوزه امری ضروری است.
با پیشرفت فناوری ها و توسعه روش های نوین خمکاری انتظار می رود که این فرآیند همچنان نقش اساسی در صنایع مختلف ایفا کند و به تولید قطعات پیچیده تر و با کیفیت تر منجر شود. توجه به استانداردهای بین المللی بهره گیری از فناوری های پیشرفته و رعایت نکات کلیدی در طراحی و اجرای فرآیند خمکاری می تواند به بهبود عملکرد و دستیابی به نتایج مطلوب در این حوزه کمک کند.
سوالات متداول
مهم ترین عامل در ایجاد برگشت فنری در خمکاری لوله چیست و چگونه می توان آن را کاهش داد؟
مهم ترین عامل در ایجاد برگشت فنری خاصیت الاستیک مواد فلزی است. مواد فلزی پس از تغییر شکل پلاستیک تمایل دارند تا بخشی از تغییر شکل الاستیک خود را بازگردانند. برای کاهش برگشت فنری می توان از روش های مختلفی استفاده کرد :
- خمکاری بیش از حد (Overbending) : در این روش زاویه خم را کمی بیشتر از زاویه مورد نظر تنظیم می کنند تا پس از برگشت فنری زاویه خم نهایی به مقدار مطلوب برسد.
- استفاده از قالب های جبران کننده (Springback Compensation Dies) : این قالب ها با طراحی خاص خود اثر برگشت فنری را به طور مکانیکی جبران می کنند.
- افزایش نیروی خمکاری : افزایش نیروی خمکاری می تواند باعث افزایش تغییر شکل پلاستیک و کاهش برگشت فنری شود. البته باید توجه داشت که افزایش بیش از حد نیرو می تواند منجر به آسیب به لوله شود.
- استفاده از مواد با مدول الاستیسیته پایین تر : مواد با مدول الاستیسیته پایین تر تمایل کمتری به برگشت فنری دارند.
- گرم کردن موضعی لوله در ناحیه خم : گرم کردن موضعی لوله می تواند باعث کاهش استحکام تسلیم و مدول الاستیسیته ماده و در نتیجه کاهش برگشت فنری شود.
چه عواملی باعث ایجاد چروکیدگی در ناحیه داخلی خم لوله می شود و چگونه می توان از آن جلوگیری کرد؟
چروکیدگی در ناحیه داخلی خم لوله ناشی از فشار زیاد و انباشتگی مواد در این ناحیه است. عوامل متعددی می توانند باعث ایجاد چروکیدگی شوند :
- شعاع خم بسیار کوچک : شعاع خم کوچک باعث افزایش فشار در ناحیه داخلی خم و احتمال چروکیدگی را افزایش می دهد.
- ضخامت دیواره لوله نازک : لوله های با دیواره نازک مقاومت کمتری در برابر چروکیدگی دارند.
- عدم استفاده از مندرل : مندرل با پشتیبانی داخلی از دیواره لوله از چروکیدگی جلوگیری می کند.
- فشار فک فشار نامناسب : فشار فک فشار ناکافی می تواند باعث حرکت لوله به سمت عقب و ایجاد چروکیدگی شود.
- روانکاری نامناسب : روانکاری ناکافی می تواند باعث افزایش اصطکاک و فشار در ناحیه داخلی خم و ایجاد چروکیدگی شود.
برای جلوگیری از چروکیدگی می توان از روش های زیر استفاده کرد :
- افزایش شعاع خم : افزایش شعاع خم باعث کاهش فشار در ناحیه داخلی خم و کاهش احتمال چروکیدگی می شود.
- استفاده از مندرل : استفاده از مندرل مناسب پشتیبانی داخلی لازم را برای دیواره لوله فراهم می کند و از چروکیدگی جلوگیری می کند.
- تنظیم دقیق فشار فک فشار : تنظیم فشار فک فشار به مقدار مناسب از حرکت لوله به سمت عقب و ایجاد چروکیدگی جلوگیری می کند.
- استفاده از روانکاری مناسب : استفاده از روانکار مناسب اصطکاک را کاهش داده و از ایجاد فشار اضافی در ناحیه داخلی خم جلوگیری می کند.
- کاهش سرعت خمکاری : کاهش سرعت خمکاری زمان بیشتری برای تغییر شکل مواد فراهم می کند و احتمال چروکیدگی را کاهش می دهد.
تفاوت اصلی بین خمکاری سرد و خمکاری گرم لوله فلزی چیست و هر کدام برای چه کاربردهایی مناسب تر هستند؟
تفاوت اصلی بین خمکاری سرد و گرم لوله فلزی در دمای فرآیند خمکاری است.
- خمکاری سرد : در خمکاری سرد فرآیند خمکاری در دمای محیط و بدون اعمال حرارت خارجی به لوله انجام می شود. خمکاری سرد برای لوله هایی با قطر و ضخامت دیواره متوسط و جنس مواد نسبتاً نرم مناسب است. مزایای خمکاری سرد شامل سرعت بالا هزینه کمتر و عدم نیاز به تجهیزات گرمایشی است. اما محدودیت هایی نیز دارد از جمله محدودیت در میزان تغییر شکل احتمال ایجاد ترک و شکستگی در مواد با استحکام بالا و برگشت فنری بیشتر.
- خمکاری گرم : در خمکاری گرم لوله قبل از خمکاری تا دمای مشخصی گرم می شود. گرم کردن لوله باعث کاهش استحکام تسلیم و افزایش قابلیت شکل پذیری ماده می شود. خمکاری گرم برای لوله های با قطر بزرگ ضخامت دیواره بالا و جنس مواد با استحکام بالا و قابلیت خمکاری پایین مناسب است. مزایای خمکاری گرم شامل قابلیت خمکاری مواد دشوار کاهش نیروی خمکاری کاهش برگشت فنری و امکان ایجاد خم های با شعاع کم است. اما معایبی نیز دارد از جمله هزینه بالاتر نیاز به تجهیزات گرمایشی و زمان بیشتر فرآیند.
به طور کلی خمکاری سرد برای تولید انبوه قطعات ساده با حجم بالا و هزینه پایین مناسب تر است در حالی که خمکاری گرم برای تولید قطعات پیچیده و با کیفیت بالا با مواد دشوار و حجم تولید کمتر مناسب تر است. انتخاب روش مناسب خمکاری بستگی به نوع ماده ابعاد لوله شکل خم مورد نظر و حجم تولید دارد.